Repair
Emergency?
Before you pull the spindle, call us. We may be able to troubleshoot. Free tech support.
Call Us
714-307-2332
Repair Department
service@hsspindles.com
Ship to Address
Address
22349 La Palma Ave.
Unit 114
Yorba Linda, CA 92887
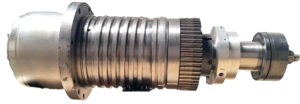
Spindle Repair
We repair all high speed spindles with automatic or manual tool change systems. We repair spindles with BT, ISO, CAT and HSK tool holding systems. We use high quality bearings (GMN) that meet or exceed the factory installed bearing specifications. All spindles are dynamically balanced to 0.3 G’s or better at full speed.
Signs of Failure
If your spindle is failing, there are usually telltale signs. It may sound different, run hotter, have more vibration or have a PLC error code. It could be a simple fix or maybe it will fail in the next few days. Feel free to call and speak with our experienced staff. We’ll help diagnose the problem while the spindle is still in operation.
Quality parts & Equipment
Engine Check Repair
24/7 Friendly Support
Our Promise:
We will follow up with a firm quote with options and completion dates. The only exception to this policy is a winding failure which can occur without warning.
We think you will find our pricing highly competitive.
Standard repairs are 4 – 5 weeks. If you need it quicker, see our expedited repair page.
All spindle repairs have a six months to a one year warranty.
Spindle Repair
Emergency? Contact us at service@hsspindles.com or 714-307-2332
Spindle Repair: We repair all high speed spindles with automatic or manual tool change systems. We repair spindles with BT, ISO, CAT and HSK tool holding systems. We use high quality bearings (GMN) that meet or exceed the factory installed bearing specifications. All spindles are dynamically balanced to 0.3 G’s or better at full speed.
Before you pull the spindle, call us. We may be able to troubleshoot. Free tech support. Signs of Failure: If your spindle is failing, there are usually telltale signs. It may sound different, run hotter, have more vibration or have a PLC error code. It could be a simple fix or maybe it will fail in the next few days. Feel free to call and speak with our experienced staff. We’ll help diagnose the problem while the spindle is still in operation.
Our Promise: Free Inspection and Firm Quote: We provide a free inspection on all spindles received. These inspections include clamp force check, run-out reading, vibration measurement and sensor functionality. In some cases, the issue is very simple; a sensor needs adjustment or an o-ring needs to be replaced. If the spindle needs further repair, we will request permission to disassemble the spindle free of charge in order to inspect the internal components.
Firm Quote: We will follow up with a firm quote with options and completion dates. The only exception to this policy is a winding failure which can occur without warning.
Fair Pricing: We think you will find our pricing highly competitive.
Length of Repair: Standard repairs are 5 – 10 business days. If you need it less than 5 days, see our expedited repair page.
Warranty: All spindle repairs have a one year warranty. Warranty does not cover winding failures.
Ship to Address: HS Spindles, LLC 22349 La Palma Ave., Unit 114, Yorba Linda, CA 92887
The quickest way to get in touch with us is to call 714-307-2332 or email our repair department at service@hsspindles.com
- Home
- Spindle Repair